Energy Industry
Energy Applications Through Nanotechnology
Microfluidizer® Processors in the Energy Industry
Efficient energy solutions are at the forefront of today’s technology and more than ever, leading companies are looking for clean energy production technologies, which are safe, reliable and cost-effective alternatives to fossil fuels. Achieving energy independence will also require storage solutions.
There are also efforts to de-carbonize our atmosphere. To achieve these goals, recent breakthroughs in nanotechnology have helped bring these unique and attractive energy applications to life. As energy companies are looking for processes that create scalable, homogenous dispersions without contamination, Microfluidics is proud to partner with leading researchers and manufacturers as they develop innovative energy solutions to help change the world.
Microfluidizer® Technology for High Performance Energy Storage Systems
Despite the advantages that carbon-based nanomaterials offer, a major issue during formulating and manufacturing is that the material tends to aggregate, which can severely decrease the specific surface areas and negatively impact performance. Contamination introduced during the manufacturing process is another critical consideration as it not only leads to the loss of electrode materials, but it also adversely affects device performance. Other challenges, associated with existing methods, include long processing times, low process efficiency, product quality and
lack of process scalability.
This application note explores how Microfluidizer® technology plays a vital role in producing High Performance Energy Storage Systems.
Homogenous Dispersions for Energy Applications
Fuel Cells
Fuel cell production is in heavy demand due to its ability to create energy electronically from fuel, such as hydrogen or methane, and air or oxygen without burning or creating environmental pollutants.
There are several different types of fuel cells depending on the type of electrolyte the employ, among which Proton Exchange Membrane (PEM), also known as polymer electrolyte membrane, fuel cells are one common type. Fuel cell production consists of two electrodes coated by an “ink,” which contains a catalyst, often noble metals, and carbon that are separated by an electrolyte. The quality of the catalyst layer, such as morphological distribution of the catalyst, is critical in determining the performance and efficiency of fuel cells.
Microfluidics has consistently demonstrated the ability to process materials used in the production of fuel cell components and other similar materials (such as inkjet inks) that require uniform particle size and high surface area. Microfluidics is the perfect partner for customers looking for a uniform, contamination-free, scalable dispersing technology to enhance their formula performance. Few homogenizer technologies can obtain the results achieved by Microfluidizer® technology.
Microfluidizer® processors help manufacturers of catalyst or electrode materials to:
- Reduce the amount of catalyst needed by increasing the surface area, thus saving money
- Efficiently achieve superior dispersion with small particle size for a better reaction
- Eliminate contamination introduction or future issues
- Address solvents related safety concerns with ATEX designs
- Create uniform electrodes for easier and more consistent post-processing
- Scale up from lab to full industrial production - unlike other methods available, Microfluidizer® technology is linearly scalable from R&D results to full production volumes
Carbon Nanotubes (CNTs)
Carbon nanotubes (CNTs) are carbon tubes that have single wall (SWCNT) or multiple walls (MWCNT) and conduct electricity. Comprised of carbon atoms held together with strong covalent bonds, CNTs have exceptional strength and flexibility and are used in a range of applications from energy storage to coatings. Microfluidizer® processors are ideally suited for the deagglomeration and dispersion of CNTs.
The Microfluidizer® technology, with its fixed-geometry Interaction Chamber™, is proven to successfully create nanodispersions with great uniformity, repeatability and guaranteed scalability - vital in CNT manufacturing.
Microfluidizer® Technology for Graphene Exfoliation
This application note gives an overview of the properties and applications of graphene. It also discusses preparation techniques and a case study executed by collaboration with the University of Cambridge to product graphene for use as conductive inks.
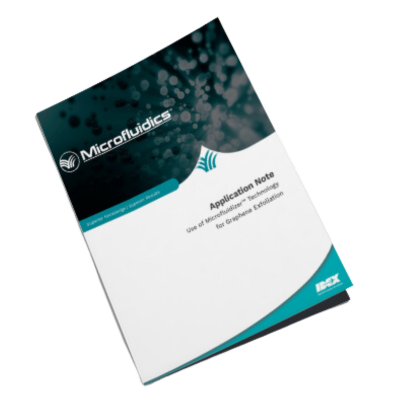
Microfluidizer® Processors for the Energy Industry
Microfluidizer® processors meet the needs of the energy industry by providing:
- The highest mixing intensity at a microliter scale to create uniform dispersions, which leads to enhanced performance
- The highest shear and impact forces, which produce a small particle size over a larger surface area
- The ability to process challenging materials
- The ability to accommodate a wide range of quantities, including expensive, low-volume samples
The Microfluidics Advantage
Easy to operate, clean and maintain, Microfluidics is the leader in high-shear processing equipment. Microfluidizer® technology ensures efficient manufacturing solutions, including:
- Achievable, uniform particle size
- Repeatable results batch-to-batch
- Seamless scalability from R&D results to commercial volumes
- Few passes for effective and cost-saving processing
- Sanitation options to prevent contamination for improved product
Microfluidics Offers a Complete Product Line
In today’s competitive world, obtaining preliminary research results is only half of the solution – finding a way to get these same results to market, quickly and efficiently, is also a challenge. Using Microfluidizer® technology, research and development formulations can be scaled up to commercialization seamlessly with proven repeatable results.
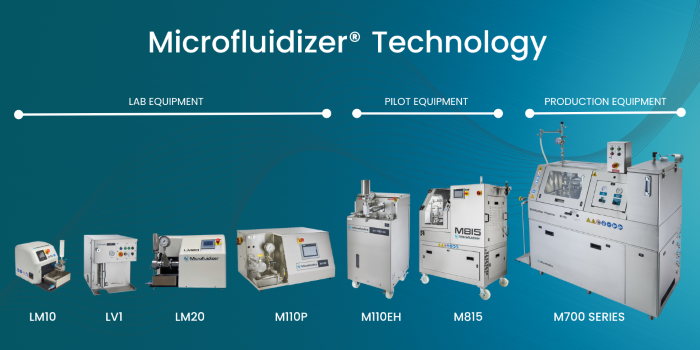